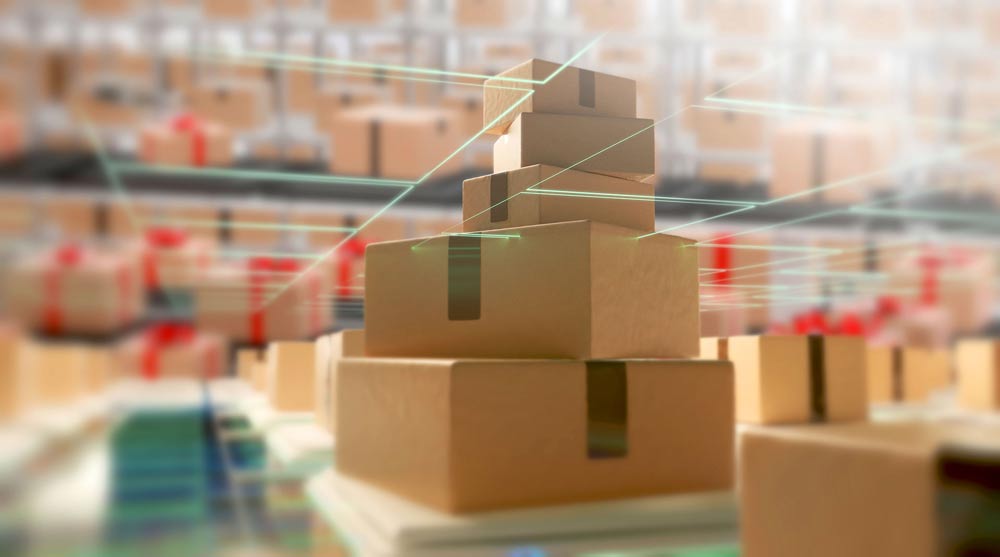
12 Jun What’s the Turnaround? Meeting Your Business Timelines in Packaging Operations
In the fast-paced world of business, timing isn’t just a factor—it’s the backbone of success, especially in the realm of packaging operations. Meeting business timelines not only boosts customer satisfaction but also sharpens the edge of supply chain efficiency and overall business performance. Let’s delve into the strategies and best practices that ensure your packaging operations are as swift as they are smooth, guaranteeing timely delivery and fulfillment of customer orders.
Understanding Turnaround Time in Packaging
Turnaround time in packaging involves several key components: order processing, production lead time, quality assurance, and shipping logistics. Each of these stages plays a crucial role in ensuring that your product not only meets quality standards but also reaches your customer without delay. Efficient turnaround times are critical—they enhance customer satisfaction, reduce inventory costs, and maximize operational throughput. It’s about keeping the gears of your business machine well-oiled and running smoothly.
Factors Influencing Packaging Turnaround Time
Several variables can tug at the seams of your packaging turnaround time. Fluctuations in order volume, material availability, equipment capacity, workforce dynamics, and production scheduling all weave into the tapestry of potential delays. Understanding these elements offers a clear blueprint for action and adjustment. For instance, securing a steady supply of materials and maintaining a flexible, well-trained workforce can mitigate many common bottlenecks.
Streamlining Order Processing and Production
The quest for quicker turnaround times begins with streamlining order processing and production. Modern solutions like automated order processing systems and optimized production schedules can dramatically reduce the time from order to delivery. Leveraging lean manufacturing principles can further enhance efficiency. Moreover, employing real-time monitoring and embracing data analytics help pinpoint inefficiencies, allowing for swift corrective actions and resource reallocation to maintain pace with demand.
Enhancing Collaboration and Communication
Never underestimate the power of good communication—especially among the teams that handle your packaging processes. Whether it’s the sales team communicating customer expectations, the production team managing the floor, or logistics ensuring timely delivery, each cog in the wheel needs to move in sync. Technology plays a pivotal role here, offering tools that enhance collaboration and ensure that every member of the team is on the same page, thus speeding up the entire packaging process.
Investing in Technology and Automation
In an era where time is currency, technology is the mint. Advanced packaging machinery, robotics, IoT-enabled sensors, and predictive maintenance systems represent just the tip of the iceberg in tech investments that can accelerate your packaging operations. These technologies not only speed up production but also improve accuracy and reduce downtime. The upfront cost of technology and automation pays off by increasing your ability to meet tight timelines and adapt swiftly to changing market conditions.
Continuous Improvement and Performance Monitoring
To stay competitive, a mantra of continuous improvement is essential. This means regular performance reviews, meticulous root cause analysis whenever delays occur, and decisive implementation of corrective actions. Cultivating a culture that values continuous learning and agility allows your business to adapt to new challenges and evolving market demands effectively.
Conclusion
Streamlining your packaging operations to meet business timelines is less about finding a one-size-fits-all solution and more about adapting to the unique rhythm of your business. It involves a symphony of strategies—from leveraging technology and fostering team collaboration to embracing continuous improvement and efficient resource management. By following these guidelines, you can ensure that your packaging operations aren’t just meeting timelines but setting benchmarks in operational excellence.
Embrace these strategies to enhance your operational agility and watch as your business not only meets but exceeds expectations, ensuring you remain a step ahead in today’s competitive market. Ready to revamp your approach? Dive into the dynamic world of optimized packaging operations and see your business thrive.
Sorry, the comment form is closed at this time.